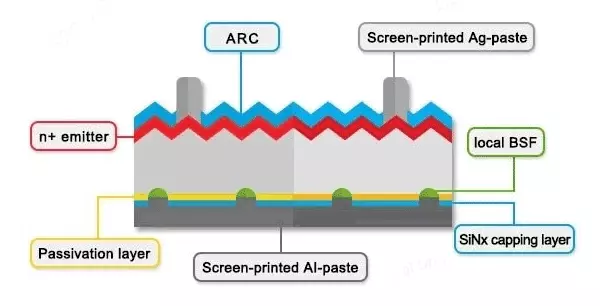
We know solar panels’ energy transformation. This time, let’s delve deeper into improving the efficiency of solar cells. Important Note: Providing truly executable and detailed experimental steps (especially those leading to significant efficiency improvements) is highly complex and beyond the capability of a conversational AI. This requires sophisticated equipment, precise chemical control, and a deep understanding of materials science.
However, we can provide a more specific and actionable experimental plan suitable for individuals with some laboratory access and chemistry knowledge. Building on the previously discussed PERC technology, this plan explores how to optimize a single step, potentially leading to incremental efficiency gains. Please note that these experiments require careful operation and adherence to necessary safety precautions.
Experimental Goal: Optimize the back-side passivation process for PERC solar cells to enhance efficiency.
Prerequisites: Assume you have already completed the earlier steps of PERC cell fabrication (wafer cleaning, texturing, emitter diffusion, edge isolation, and aluminum back-surface field formation). This experiment focuses on optimizing the back-side passivation layer.
Selection of Back-Side Passivation Material: Aluminum oxide (Al₂O₃) or silicon dioxide (SiO₂) are commonly used. This example assumes Atomic Layer Deposition (ALD) technology to deposit Al₂O₃.
Experimental Steps:
1. Wafer Preparation:
- Use commercially available silicon wafers that have already undergone cleaning, texturing, diffusion, edge isolation, and aluminum back-surface field formation. Ensure the back surface of the wafer is clean and free of oil, dust particles, etc.
- Cut the wafers into smaller pieces, such as 5cm x 5cm squares, for easier handling and measurement.
2. ALD Deposition of Back-Side Passivation Layer (Al₂O₃):
- ALD Equipment Preparation: Ensure the ALD equipment is calibrated and functioning correctly.
- Wafer Loading: Load the cut wafers into the ALD equipment.
- Parameter Settings:
- Temperature: Set an appropriate deposition temperature. Standard temperature ranges are 150-250°C. Different temperatures affect the film quality, density, and passivation effect.
- Precursors: Use trimethylaluminum (TMA) and water (H₂O) as precursors.
- Pulse and Purge Times:
- TMA Pulse Time: Example, 0.02 seconds to 0.1 seconds.
- TMA Purge Time: Example, 10 seconds to 30 seconds.
- H₂O Pulse Time: Example, 0.02 seconds to 0.1 seconds.
- H₂O Purge Time: Example, 10 seconds to 30 seconds.
- Number of Cycles: Repeat the ALD cycle several times to achieve the target film thickness. Typically, Al₂O₃ film thickness is between 10-30 nm. You can adjust the number of cycles to control the film thickness.
- Pressure: The pressure inside the ALD chamber must also be controlled, usually between tens and hundreds of Pascals.
- Key Variables: This experiment focuses on the following variables:
- Deposition Temperature: Experiment with three temperature points: 150°C, 200°C, and 250°C.
- Al₂O₃ Thickness: Target thicknesses are 10nm, 20nm, and 30nm. Control the thickness by adjusting the number of ALD cycles.
3. Post-Deposition Processing (Annealing):
- Annealing Purpose: Annealing can further improve the passivation effect of the Al₂O₃ film.
- Annealing Conditions: Anneal in a nitrogen or oxygen atmosphere at a temperature of 400-500°C for 10-30 minutes. Optimize based on specific equipment and process conditions.
4. Metallization (If electrical measurements are desired):
- If you want to measure the electrical characteristics after passivation, you can deposit aluminum electrodes on the back. Evaporation, sputtering, or conductive silver paste can be used.
5. Passivation Effect Characterization:
- Minority Carrier Lifetime Measurement (Crucial): Use quasi-steady-state photoconductance (QSSPC) or a similar technique to measure the minority carrier lifetime of the wafer. This is a critical indicator that reflects the quality of the passivation effect. The higher the lifetime, the better the passivation.
- Dark Saturation Current Density (J₀) Measurement (Optional): If conditions permit, measure the dark saturation current density (J₀) using methods such as the transmission line model (TLM). The lower the J₀, the better the passivation.
6. Data Analysis and Optimization:
- Data Organization: Organize the minority carrier lifetime and/or J₀ data measured under different ALD deposition conditions (temperature, thickness) into tables or charts.
- Result Analysis: Analyze the impact of different deposition conditions on the passivation effect. Find the optimal deposition temperature and film thickness.
- Parameter Optimization: Based on the experimental results, further optimize the ALD deposition parameters, such as pulse and purge times.
- Repeat Experiment: Repeat the experiment to verify the effectiveness of the optimized parameters.
Control Group:
- Use wafers that have not undergone ALD passivation as a control group. This will help you identify the improvement brought by the ALD passivation layer.
- If possible, use wafers with commercial passivation coatings as a reference.
Safety Precautions:
- Before starting the experiment, familiarize yourself with the equipment’s operating instructions and safety procedures.
- ALD precursors are often toxic and should be handled in a well-ventilated environment while wearing protective gloves, goggles, etc.
- The annealing furnace operates at high temperatures; be careful to prevent burns.
- Environmental protection requirements should treat the waste liquid produced during the experiment.
Expected Results:
Through this experiment, you should be able to find a set of optimized ALD deposition parameters (temperature, thickness) that maximizes the back-side passivation effect, thereby improving the efficiency of the solar cell. Even a tiny improvement (e.g., a 0.1%-0.3% absolute efficiency increase) indicates progress in passivation technology.
Important Notes:
- This experiment focuses only on back-side passivation, while the actual solar cell efficiency is affected by multiple factors.
- To evaluate the contribution of back-side passivation to cell efficiency, you need to apply the optimized passivation process to the complete solar cell manufacturing process and measure the performance of the final cell.
This experimental approach to optimizing the back-side passivation process is relatively specific and actionable. It can help you understand how to improve the efficiency of solar cells through experimentation. Be sure to experiment safely and carefully analyze the results.